Our Products and Services
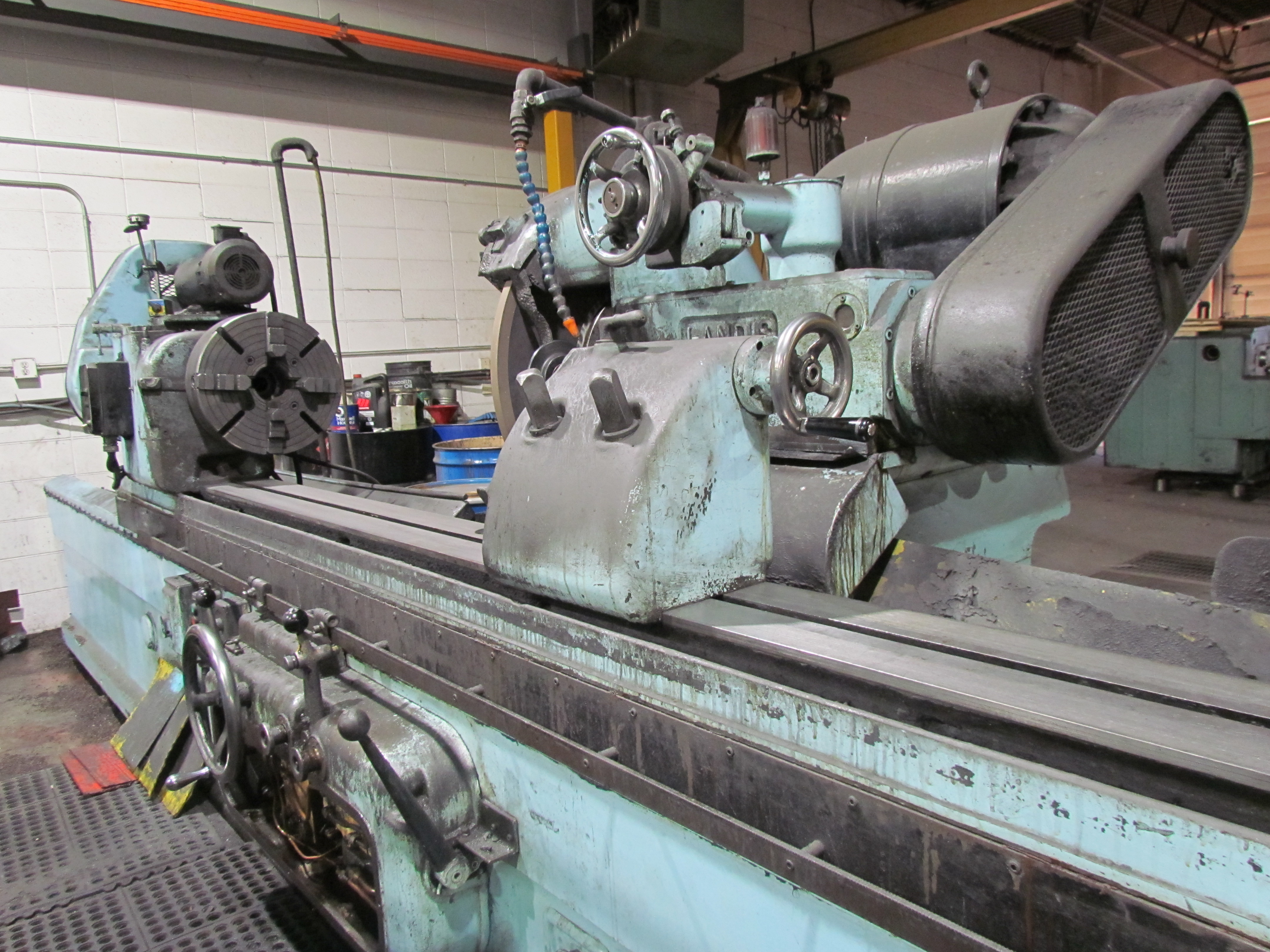
Machining Processes
Surtek has equipment which enables us to manufacture high-quality products capaciously in a cost competitive industry. Even minimal quantity orders are welcome.
We also offer straightening and other hydraulic press applications.
Capacities:
- Manual Machining Lathes: capacity 22" x 120"
- Manual Milling: capacity 13" x 60"
- 100 Ton Straightening Press: capacity 8" x 25'
- Shaft Polishing: capacity 20" x 20'
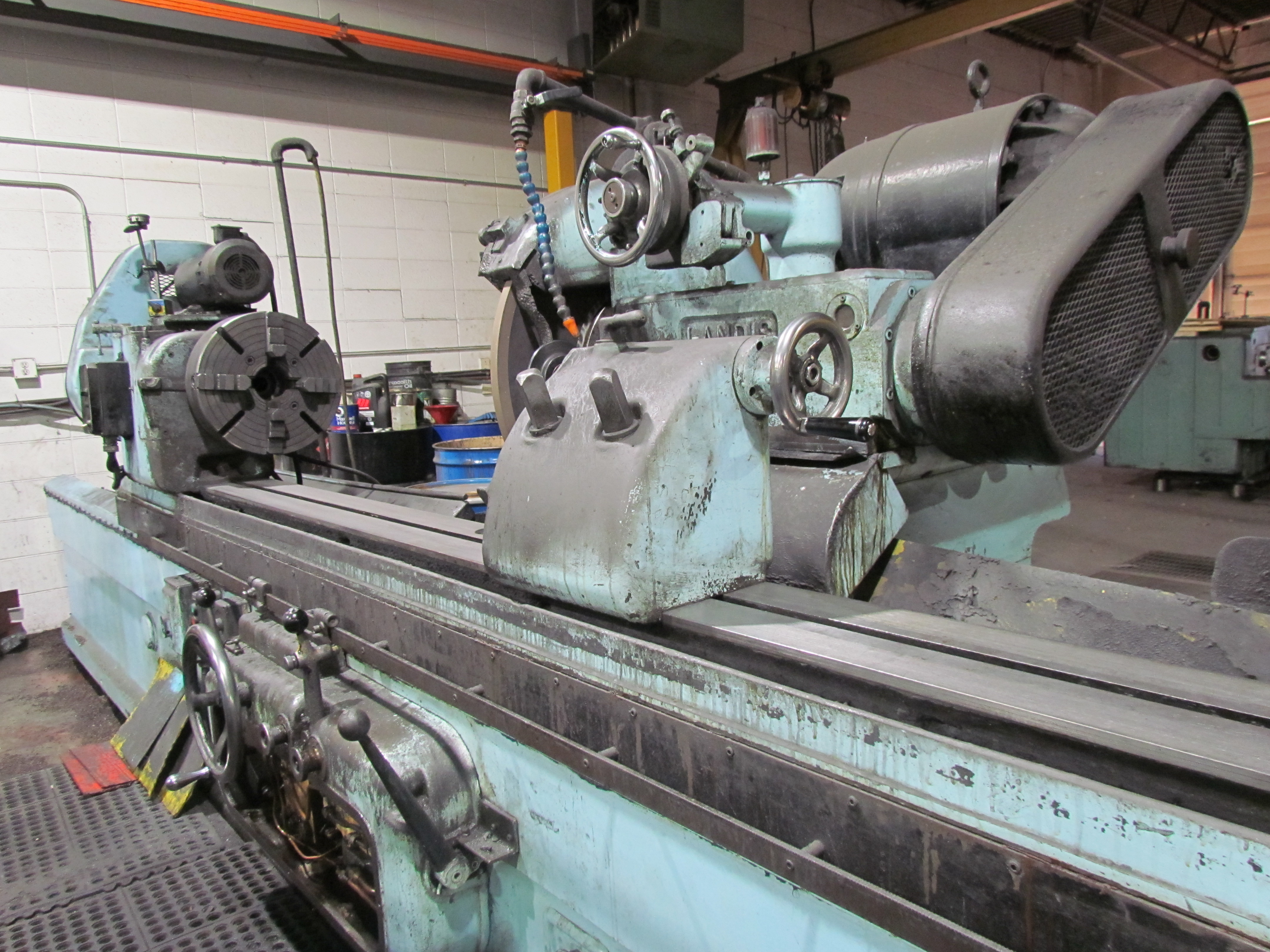
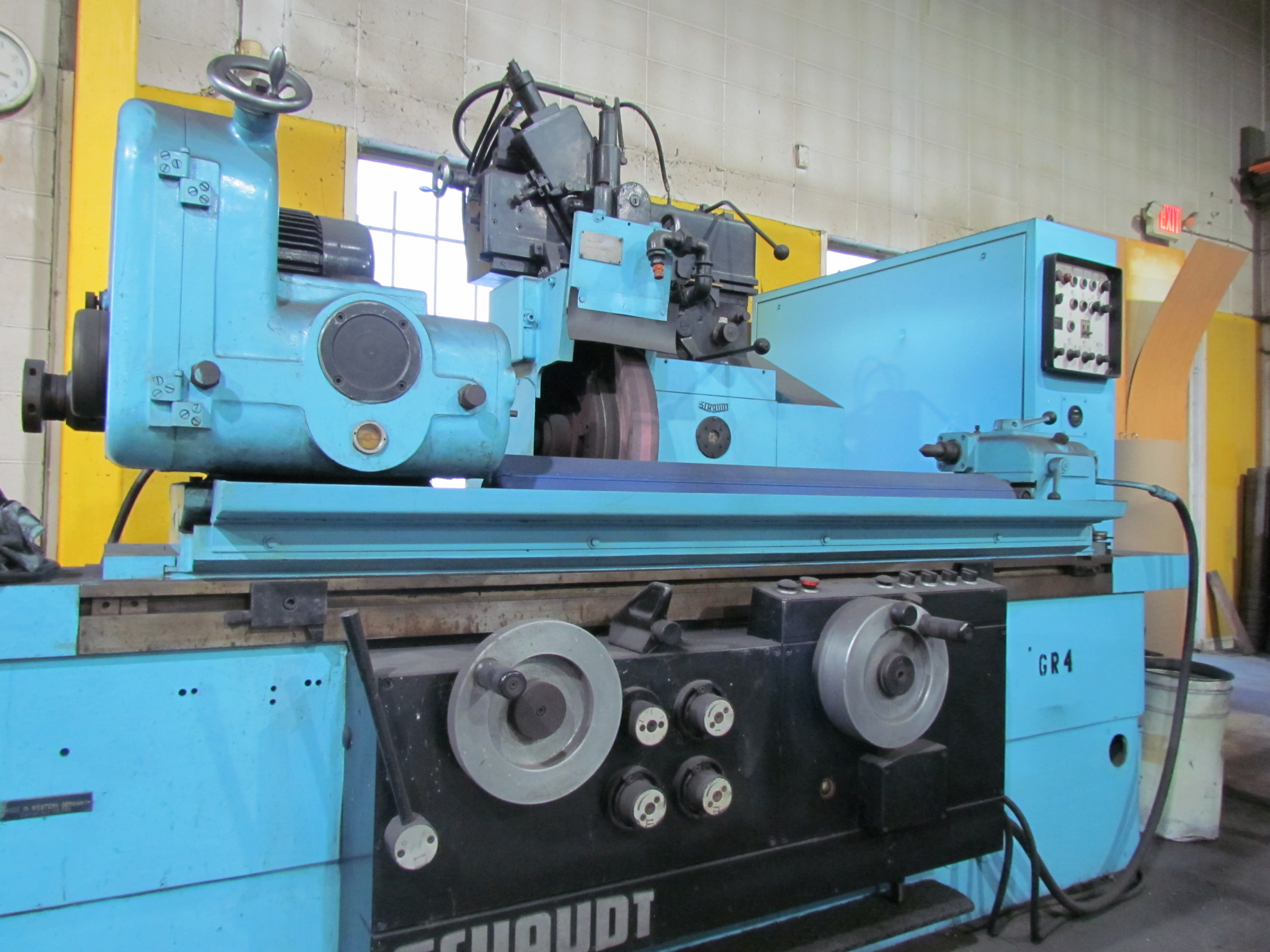
Grinding Services
A full line of cylindrical grinders and supporting equipment allow us to service most customer requirements. Tolerances of +/- .0001 are often required and achieved by grinding. Surface finish requirements to mirror finish Ra values are routinely met by diamond polishing.
Capacities:
- O.D. Cylindrical Grinding: capacity 22" x 120"
- Surface Grinding: capacity 16" x 60"
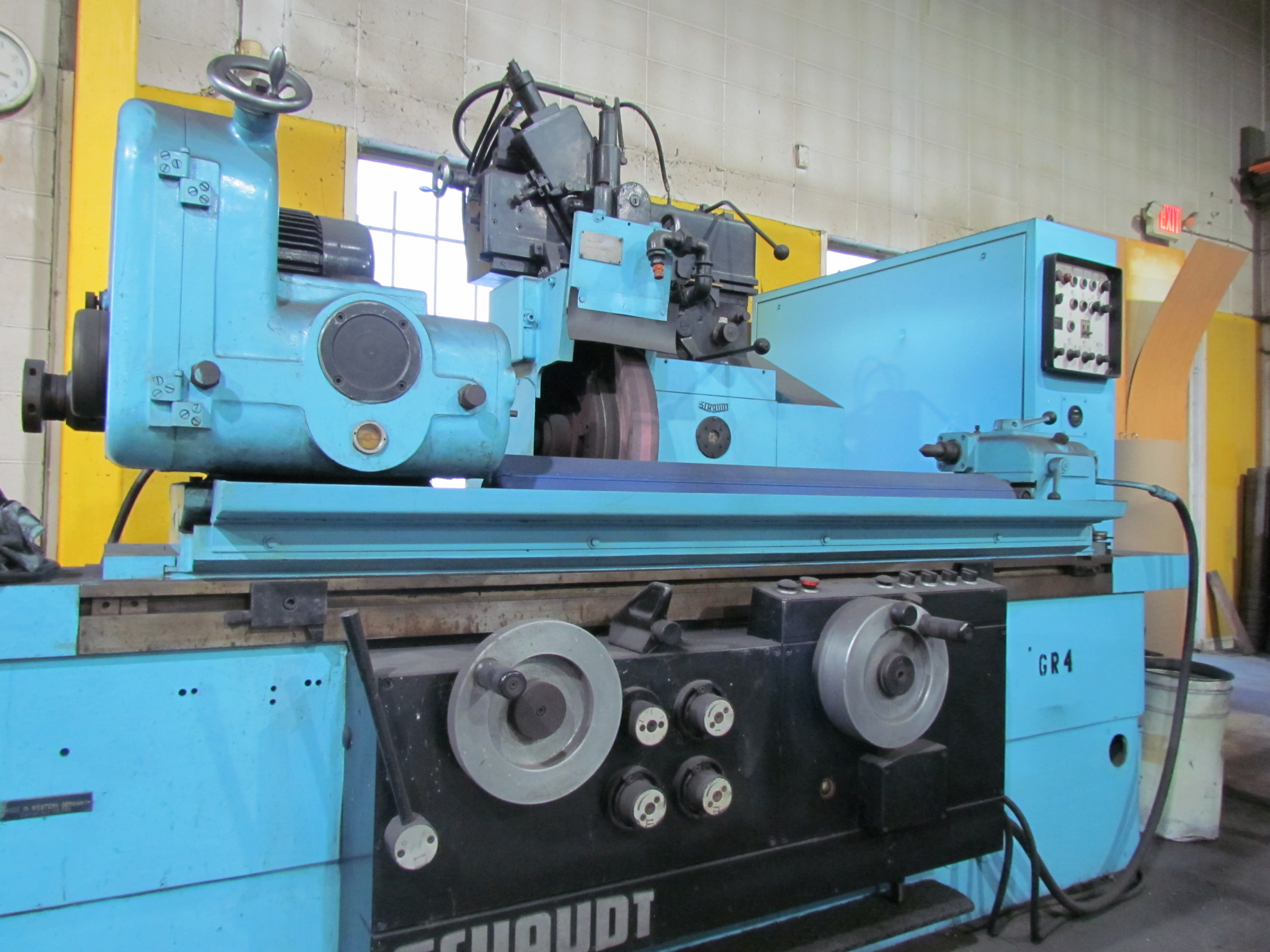
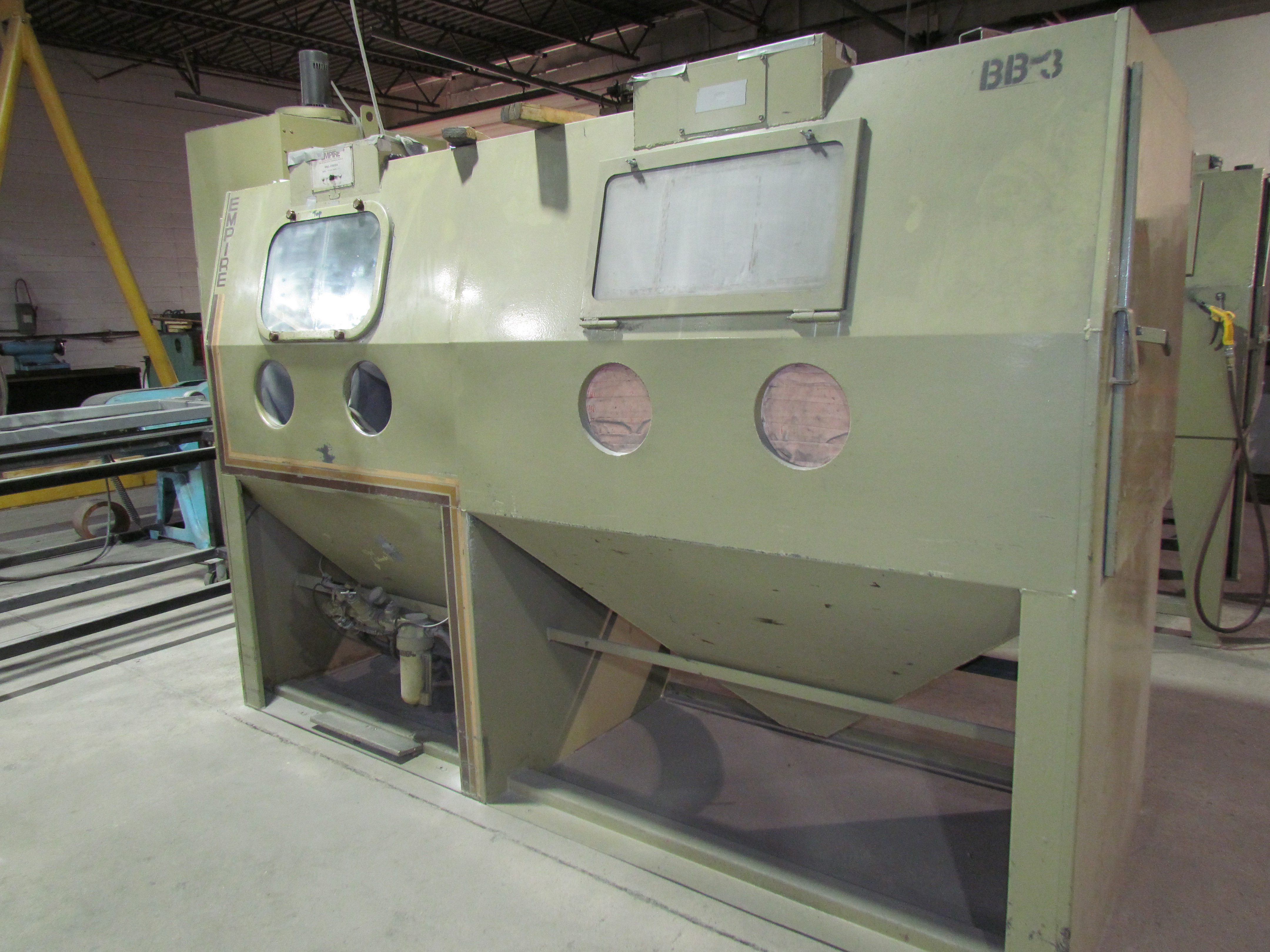
Surfacing: Shotpeen and Glass Bead
Various shot sizes are offered in our controlled shotpeen process. Shotpeen & glass bead are repeatable processes that can:
- Increase fatigue life and strength
- Reduce galling
- Help promote an even surface compressive stress layer
- Provide consistent and repeatable surface finishes
- Work harden surfaces
- Inhibit susceptibility to stress corrosion cracking
Capacities:
- Controlled Shotpeening: 96" enclosed
- Glass Bead Blasting: 96" enclosed
- Aluminum Oxide Abrasive Blasting: 105" enclosed
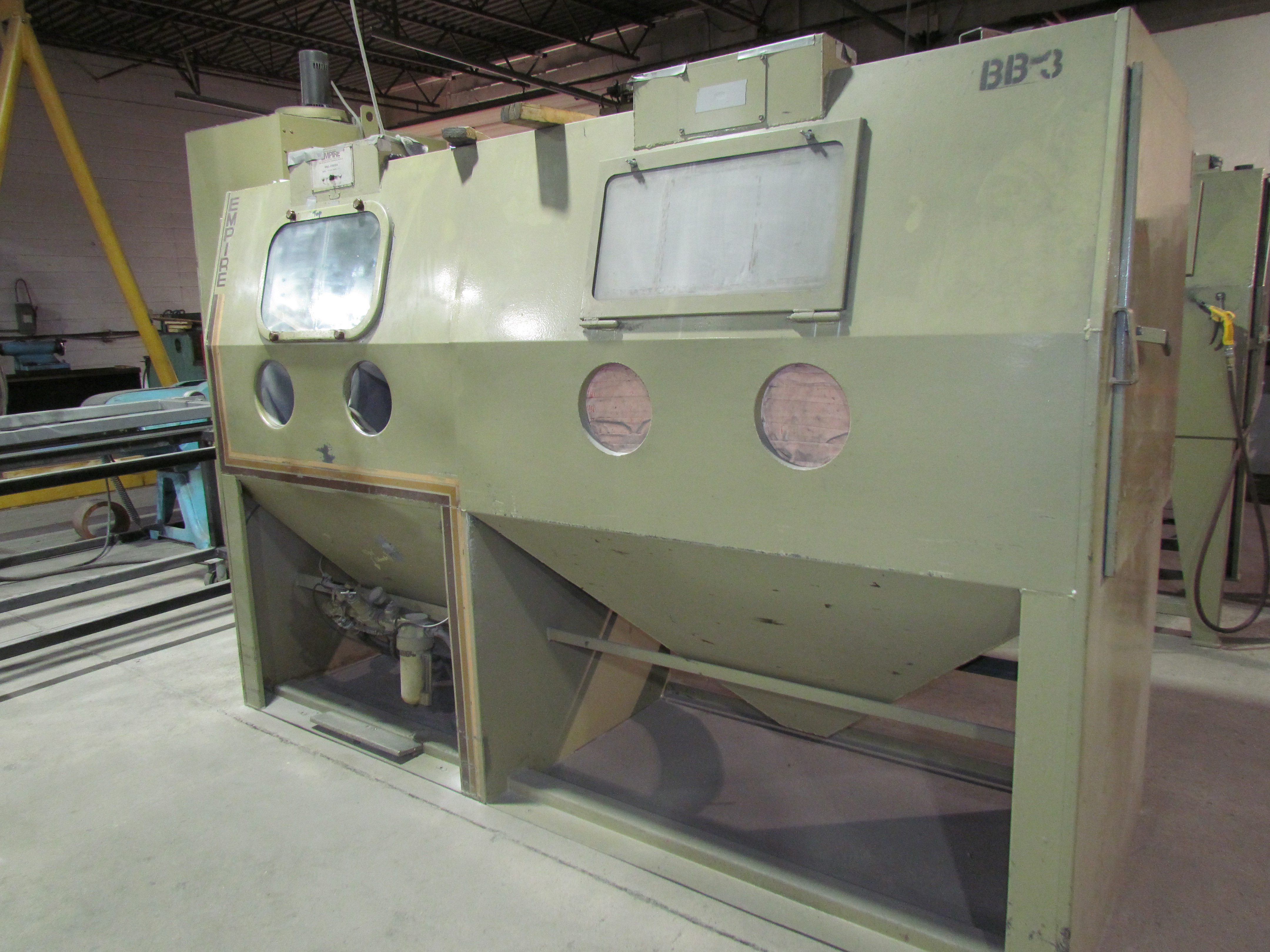
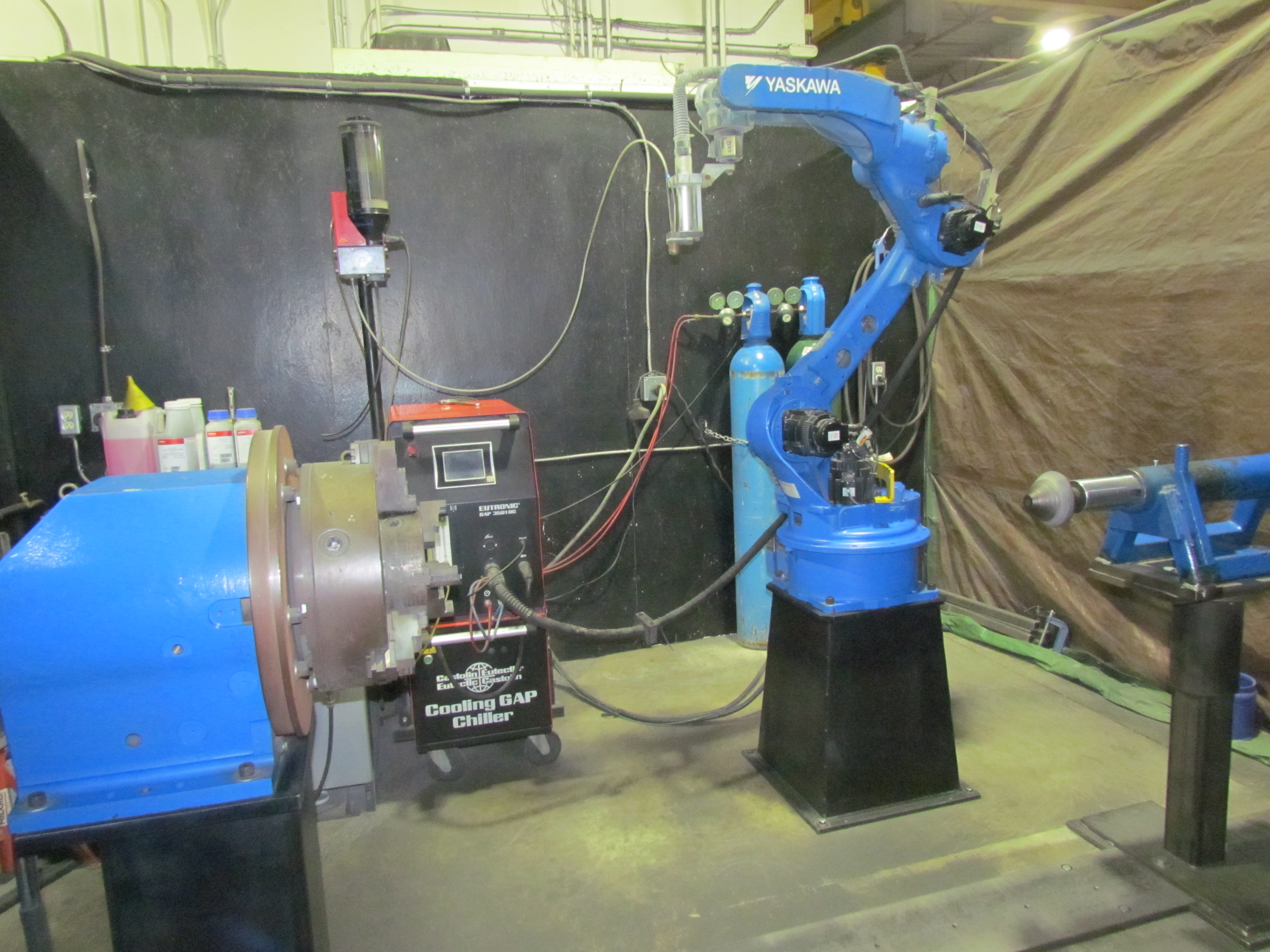
Plasma Transferred Arc Welding
Are you looking for a more economical way to overlay your components with a metallurgical bonded, high hardness, corrosion resistant, or high-wear metal matrix material? Surtek Solutions Inc. offers Plasma Transferred Arc (PTA) process that may be the solution for you with up to 20% savings over laser cladding, GTAW and other solutions. PTA is a versatile method of depositing high quality strongly fused deposits on a wide range of base materials:
- Carbon Steel
- Non-Magnetic Super Austenitic Alloys
- Nickel Alloys
- Soft Alloys
- Medium and High Hardness Materials
- Carbide Composites
With PTA we can achieve diverse properties such as:
- Improved Mechanical Strength
- Wear Resistance
- Galling Resistance
- Corrosion Resistance in various working environments
PTA especially excels in powder alloys that are too hard to draw into wire and metal matrix composites where an extremely hard material, such as Tungsten Carbide (WC), is applied together with a binder material like Nickel. In most applications, the PTA process is able to apply the same materials at the same quality as the other welding and thermal spray processes, at a significant cost savings due to PTA’s reduced operating and ownership costs.
PTA’s lower heat input allows the process to achieve the required overlay properties in wide range layer thickness. The capability of producing a low dilution, porosity free overlay allows the PTA process to achieve a higher quality product using much less material and with drastically less heat input into the base material.
Possible Applications:
- Hard Surfacing o PTA is well suited to apply hard alloys for wear resistance. Stellite, Colmonoy, Hastelloy, and Tungsten Carbide can all be successfully applied with PTA.
- Corrosion Resistant Overlays. The localize heat input characteristics of PTA allows corrosion resistant alloys to be applied with very little dilution into the base material.
Industries / Components:
- Non-Magnetic Down Hole Tools, Drill Collars, Wear Bands for MWDs
- Down Hole Components: Mud Motor Bearings, Stabilizers, Topsubs, Piston Subs, Flow Restrictors, Drill Bits
- Flow Control: Valve Bores, Gates, Seats, Seat Pockets, Ring Grooves, Valve Stems
- Power Generation: Turbine Blades, Shafts, Bearing Surfaces
- Riser Equipment, Pins, Boxes
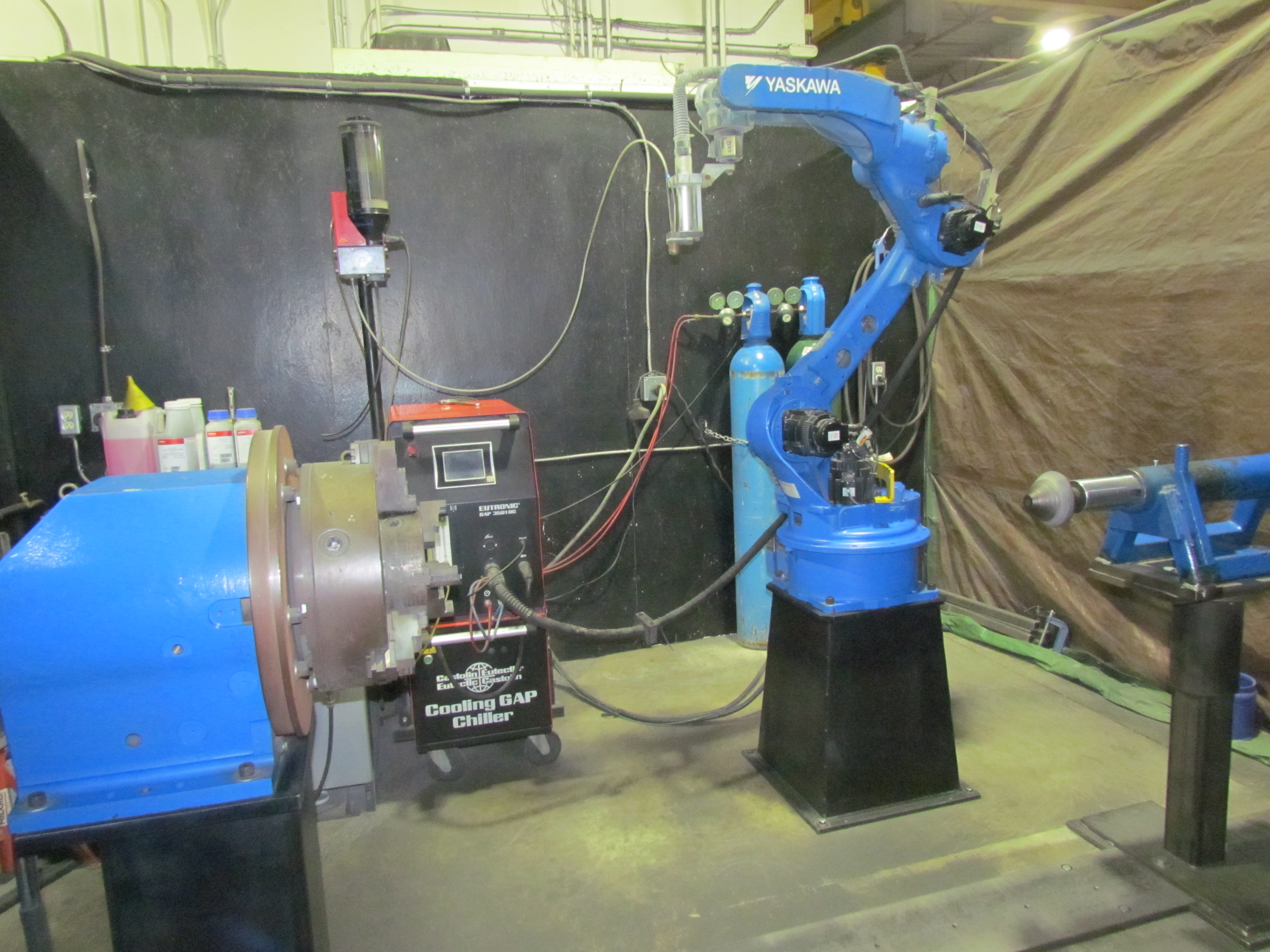
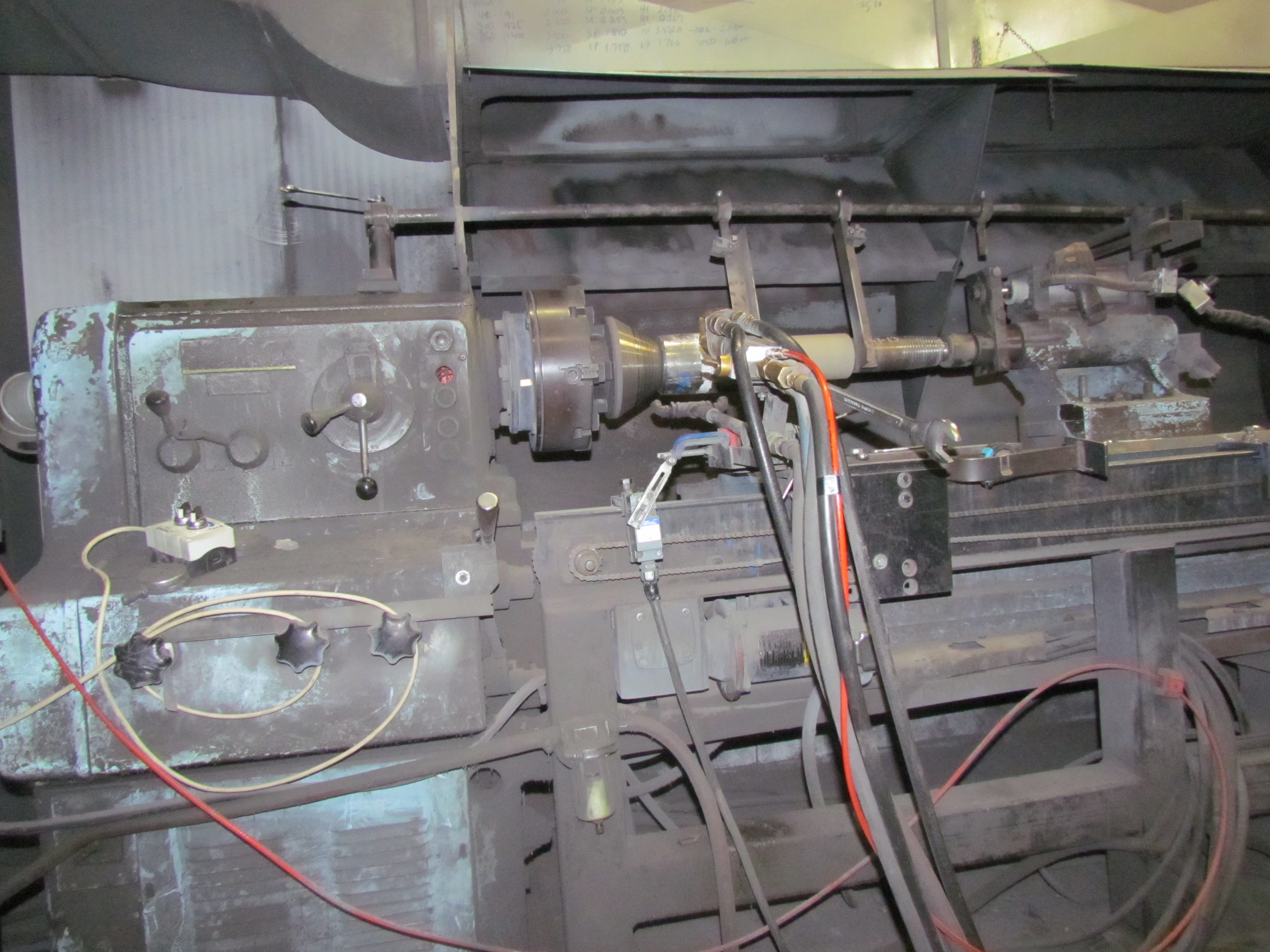
Thermal Spray Technology
Thermal spray is a generic term for a group of processes that utilize a heat source to melt material in powder, wire or rod form The molten or semi-molten mate-rial is propelled toward a prepared surface by expanding process gases. The particles quench rapidly upon impact with the surface and bond with the part.
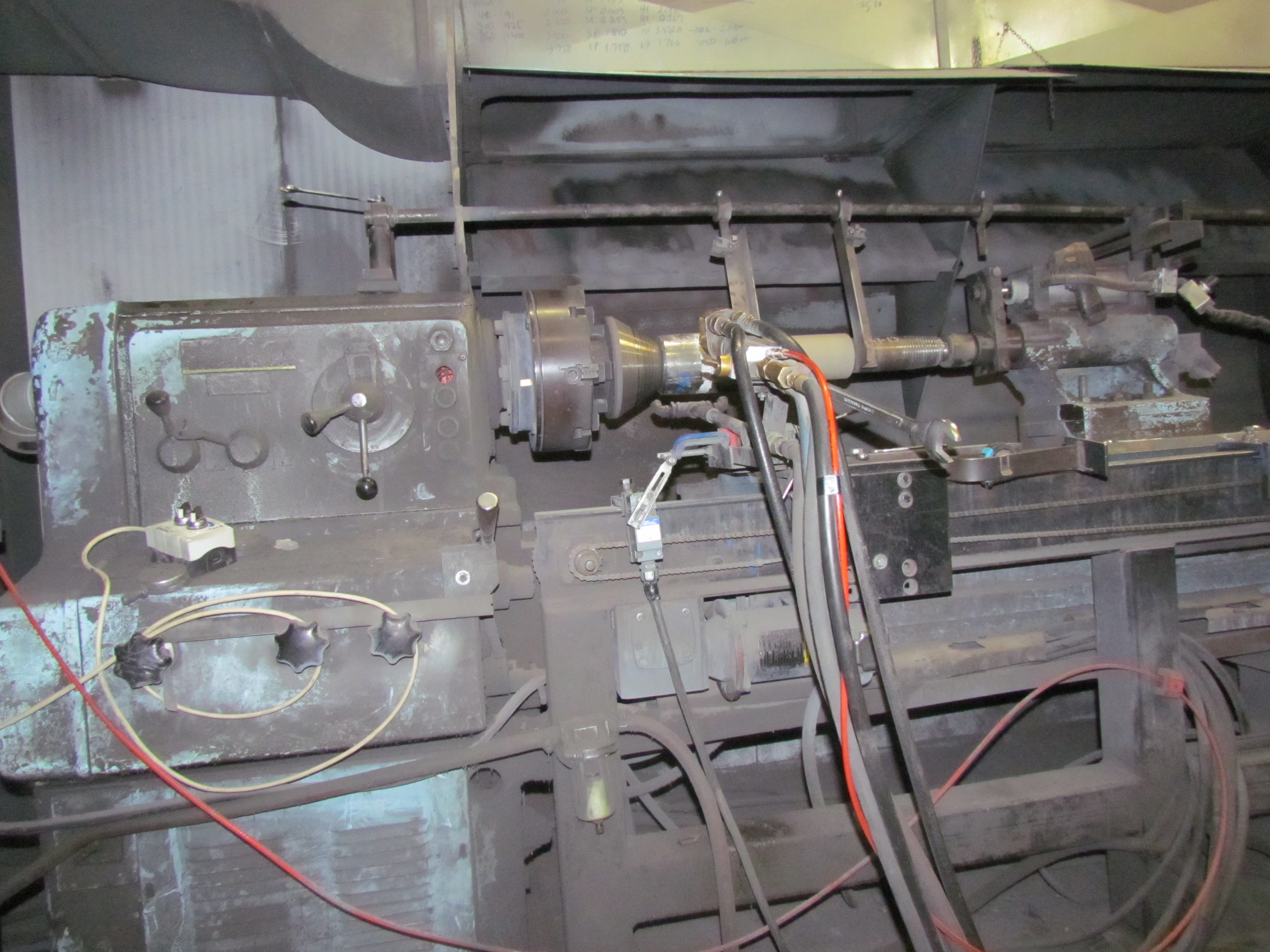
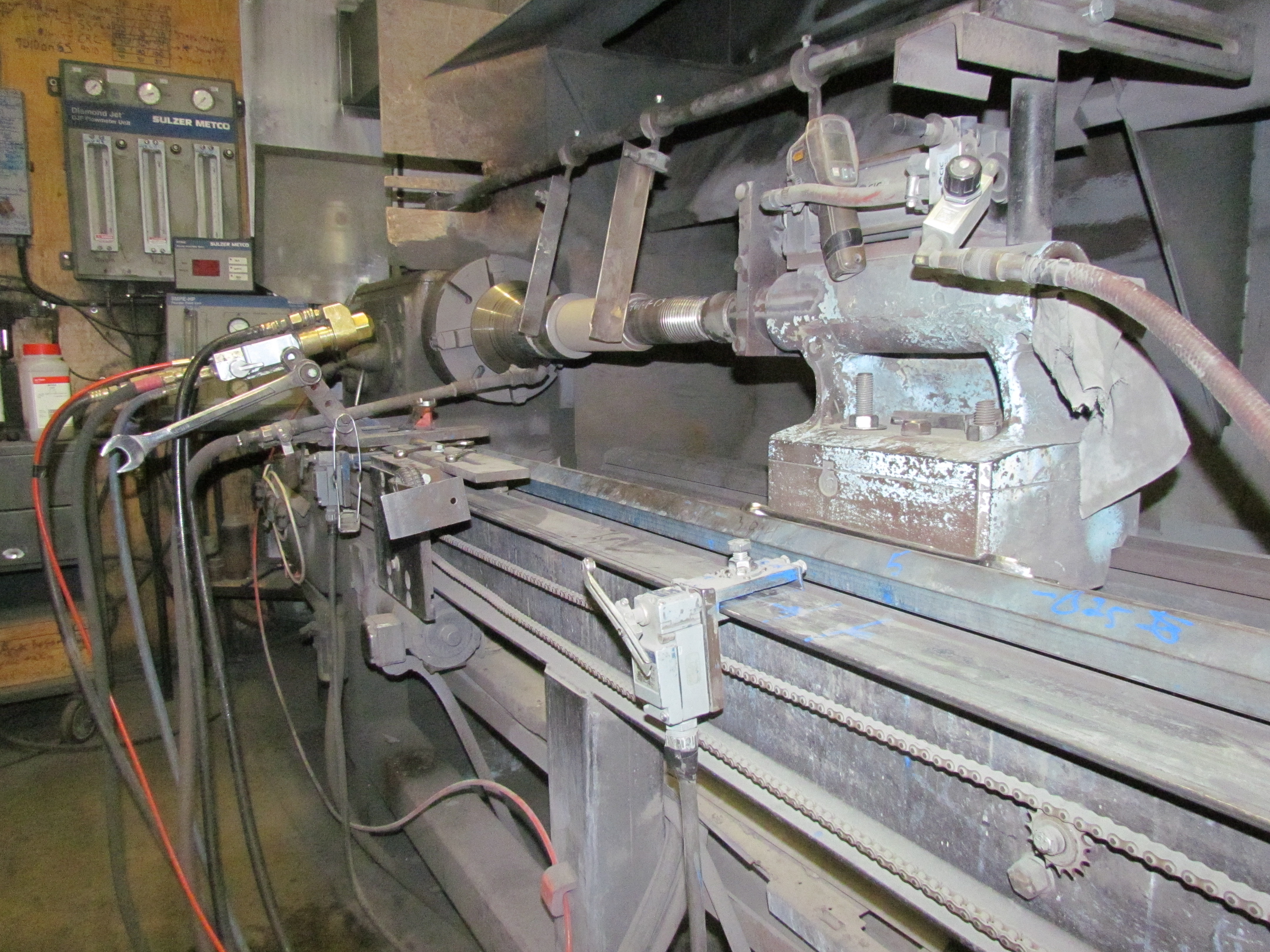
HVOF (High Velocity Oxy-Fuel)
HVOF coating systems were developed in order to produce coatings with superior bond strength, higher density and higher hardness than other spray processes. Using HVOF, an oxygen-fuel mixture is continuously fed under pressure into a combustion chamber where gases are ignited and channelled into a nozzle. Material is introduced axially or radially into the combustion stream and accelerated onto the substrate at velocities up to 1975 feet per second.
High Velocity Oxy Fuel (HVOF) has been successfully used for:
- Bottom-Hole Pump Plungers and Rotors
- Valve Gates and Seats
- Mud Motor Flow Collars
- Drive Shafts
- Pump Jacks
- Hydraulic Components
- Down-hole Drilling and Pumping Tools
- Rotating Seal Elements
- PC Pump Surface Drive Shafts
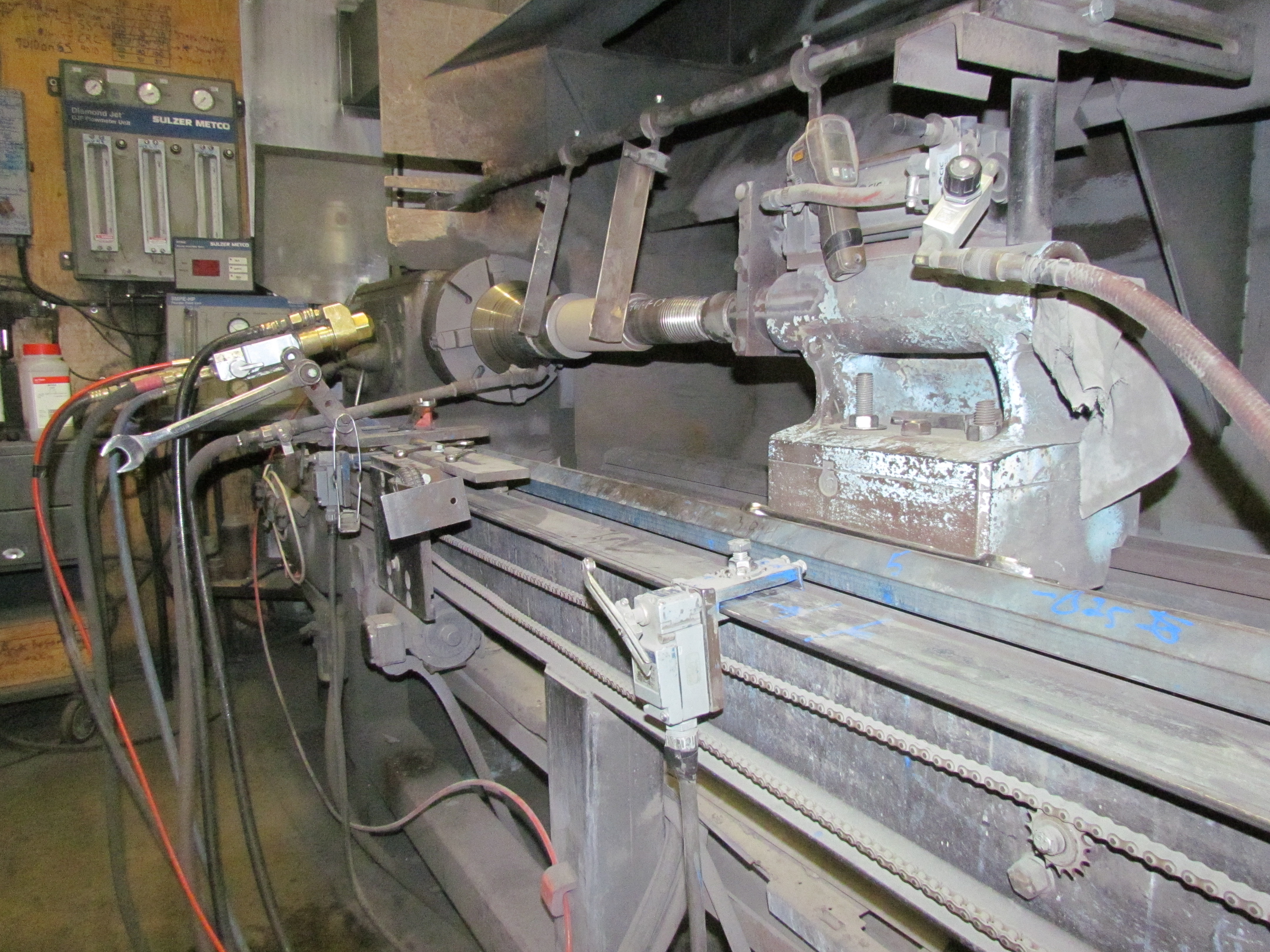