News and Innovation
The applicators of thermal sprayed coatings have been looking for methods to apply thicker, porous-free coatings. Harmful residual stresses always were a problem for coatings thicker than 0.020" (0.5 mm) applied with gas-fuel HVOF systems. Surtek Solutions Inc. successfully conducted a research project "The Improvement of Thermal Spray Working Characteristics" and, as a result, developed a reliable method to apply thick coatings providing better corrosion and wear resistance. This research project was supported by NRC Industrial Research Assisstance Program (IRAP). The main idea of our method is the oxidation suppressing of Cr, Co, and Ni by means of using a special additives to the thermal spray powder.
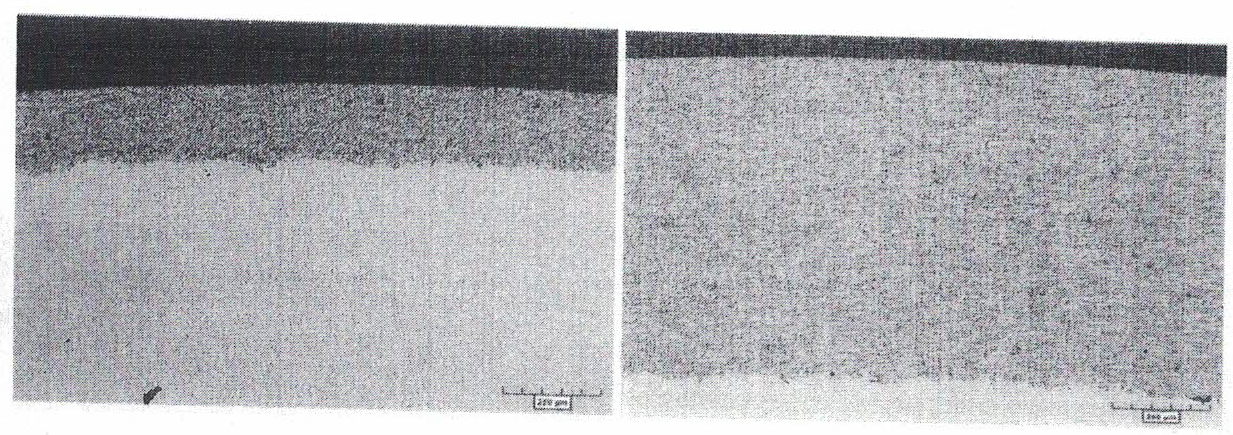
Left: Standard HVOF coating WC-10%Co-4%Cr Thickness 0.008" (0.2mm), Porosity 1%.
Right: Surtek Solutions Inc. HVOF coating WC-10%Co-4%Cr Thickness 0.040" (1 mm), Porosity 0.1%.
The right picture displays the coating of increased thickness that was sprayed using the method, comparing to the coating of standard thickness that is shown on the left picture.
Ideal Hard Chrome Replacement
Recent changes in regulations have promulgated new and more stringent rules to limit hexavalent chrome releases to the environment. These rules have increased the cost and complexity of hard chrome plating.
HVOF (high velocity oxygen fuel) coating technology has developed the point where it is typically superior to chrome. According to the Hard Chrome Alternatives Team (HCAT), in general it is found that the performance of HVOF coatings is far superior to chrome in wear, fatigue, and impact resistance. Additionally it is at least equal in corrosion resistance. Furthermore, the HVOF deposition process has a quicker turnaround time than chrome (typically an hour or two versus 24 hours). HVOF coatings also do not require the embrittlement relief which chrome processes often do. Its improved performance lowers the expected overhaul frequency thereby reducing the lifetime cost of ownership.
Controlled Shot Peening
CSP Surtek ©
Shot peening of steel parts is a very effective manufacturing method for increasing of fatigue resistance of parts.
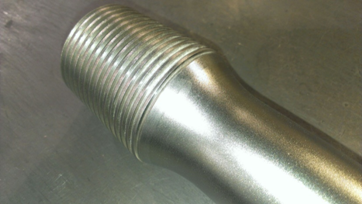
It works like a wrist bandage of an athlete which supports muscles by compression and allows them to endure the most severe stresses during exercises. In the same manner, circumferential shot peening of a diameter increases the endurance against cycling loads.
The quality of shot peening is characterized by its intensity, the standard parameter that describes depth and strength of compressive stresses in metal. The formations of beneficial compressed residual stresses are a result of the shot peening process.
Surtek Solutions Inc. introduced a proprietary method of shot peening control. The Patent Application #2,876,806 for this invention “Method and System for Characterizing a Shot Peening Process” was filed in the Canadian Intellectual Property Office on January 7, 2015. The method includes all existing industrial requirements for the quality of shot peening process mentioned in widely popular technical Standards and Norms, namely:
- AMS 2430N
- Shot Peening, Surface Engineering, Vol.5, ASM handbook, 10th Ed.
- MIL-S-13165C
The SPC Surtek © method is based on the measuring system that measures and analyses two parameters: speed of shot particles and mass of shots during the process.
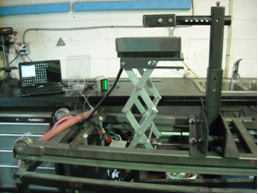
Calculating device comprising of analog-digital transmitter (ADT) and printed circuit board (PCB) calculates the optimum shot peening distance, capacity of shot flow at this distance and saves the data in computer’s memory. Then operator inputs the process requirements from the customer spec for the certain part to be processed, for instance:
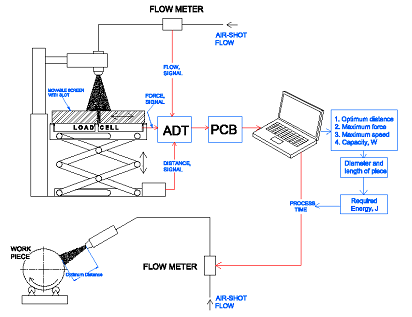
- Geometrical parameters of shot peened area (diameter, length, angle, etc.)
- Type of shots (media type, hardness, size)
- Air pressure
- Type of nozzle
- Required intensity in Almen strip arc values and type of Almen strip
- Coverage in percent
- Work piece speed movement in rotation and translation
As a result, the system calculates and displays the energy or work in Joules and time required for obtaining the pointed intensity. When operating advanced CNC-controlled shot peening systems, the calculated parameters are programmed. With manual shot peening shot peening apparatus, the operator keeps the required optimum distance using a laser distance indicator.
The application of SPC Surtek © system allows us to ensure the supreme quality of our shot peening by providing: 1. Uniformity of shot peening intensity across the part’s surface including threads, grooves and diameter transitions. 2. Consistency of required shot peening parameters (intensity, coverage) through all the parts of the order. 3. Assured level of residual compressive stresses in depth and any direction across the surface.
SPC Surtek© measuring system with protective hood in shot peening cabinet.
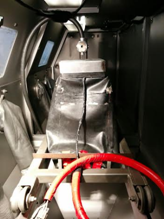
Force-Distance diagram for optimum working distance diagram for optimum working distance, shot speed and energy calculation.
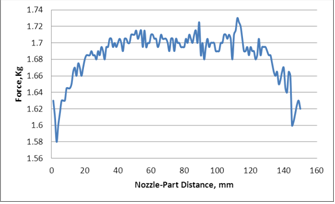